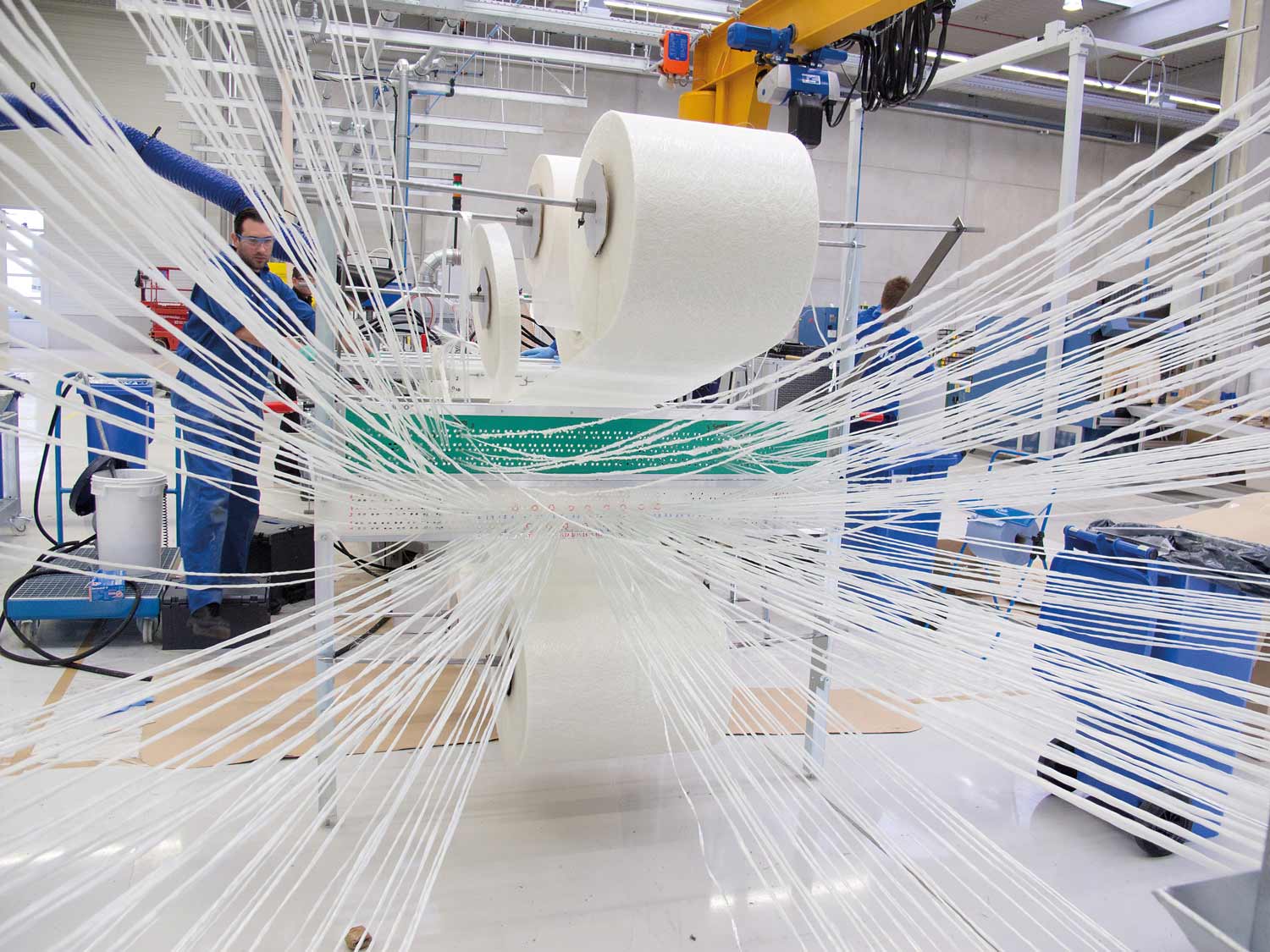
Nos méthodes de production
La pultrusion
La pultrusion est une technologie de production linéaire permettant de créer des profilés composites à section constante. Ce procédé, unique parmi les différentes méthodes de transformation des matériaux composites, se distingue par son fonctionnement continu. Le terme "pultrusion" provient de la combinaison des mots anglais "to pull" (tirer) et "extrusion". Apparue après la Seconde Guerre mondiale, cette technique offre une alternative ou un complément aux procédés comme le filage de l'aluminium, l'extrusion des thermoplastiques, le profilage des métaux, ou encore le travail du bois.
Malgré une part de marché relativement modeste (2 à 3% du marché mondial des composites, soit environ 200 à 300 000 tonnes de matières transformées chaque année), la pultrusion figure aujourd'hui parmi les technologies les plus prometteuses en termes d'innovation et de croissance dans le secteur des matériaux composites.
Une technologie aux possibilités infinies pour les composites
La pultrusion permet de combiner une large variété de renforts (fibres de verre, carbone, kevlar, basalte, etc.) et de matrices polymères (résines, pigments, additifs), offrant ainsi des possibilités quasi illimitées aux concepteurs. Les profils obtenus peuvent atteindre un taux de renfort impressionnant, allant jusqu'à 70% en masse, avec une orientation des fibres parfaitement maîtrisée. Ce niveau de précision garantit des propriétés mécaniques exceptionnelles et une durabilité remarquable des produits finis.
En raison de son haut degré d'automatisation, la pultrusion permet de concevoir des géométries complexes à des coûts compétitifs, ce qui la rend particulièrement adaptée à la production en série ou à grande échelle.
Les étapes clés du procédé de pultrusion
- Imprégnation des renforts : Les fibres (rowing, mat, tissus) sont imprégnées d'une résine polymère, enrichie de charges minérales, pigments ou additifs selon les besoins.
- Préformage : Les renforts imprégnés passent dans une station de préformage, où leur configuration stratifiée est ajustée pour répondre aux spécifications techniques.
- Polymérisation : Les matériaux passent ensuite dans un moule chauffé où la résine durcit par polymérisation. Ce processus chimique transforme les molécules en un matériau composite solide et homogène.
- Traction continue : Un mécanisme spécifique (chenilles ou chariots alternés) exerce une traction régulière, permettant au profilé de se consolider sans déformation ni ruptures.
- Découpe automatique : Le profilé final, désormais solide et parfaitement formé, est coupé sur mesure, prêt pour son utilisation finale.
Les avantages de la pultrusion
Grâce à sa nature continue, le procédé de pultrusion offre une productivité élevée et une grande régularité dans la qualité des produits fabriqués. Il constitue une solution particulièrement économique pour les projets nécessitant des volumes importants, tout en répondant aux exigences de durabilité et de performance mécanique.
LE PULLWINDING
Le pullwinding est une technique spécialement conçue pour la fabrication de profilés cylindriques ou tubulaires. Ce procédé est principalement utilisé pour produire des pièces présentant une symétrie de révolution, telles que des tuyaux, tubes, réservoirs ou bouteilles de gaz. Grâce à sa précision et sa flexibilité, il répond aux exigences de nombreux secteurs industriels.
Les étapes du procédé de pullwinding
La fabrication d'un profilé pullwindé repose sur l'enroulement de fibres imprégnées de résine catalysée autour d'un mandrin cylindrique en rotation, qui sert de moule intérieur. Les fibres de renfort, généralement en verre, peuvent être disposées selon différents axes en fonction des propriétés recherchées pour le produit fini. Ce positionnement des fibres permet de générer des stratifications spécifiques, selon trois types principaux d'enroulement : circonférentiel, hélicoïdal et polaire.
- Enroulement circonférentiel : Dans cette configuration, les fibres sont enroulées à 90° par rapport à l'axe du mandrin. Ce type d'enroulement offre une excellente résistance tangentielle, mais au détriment de la résistance longitudinale.
- Enroulement hélicoïdal : Pour équilibrer les propriétés mécaniques, l'enroulement hélicoïdal combine des fibres orientées longitudinalement et en biais par rapport au mandrin. Cet angle est ajusté grâce au mouvement coordonné du guide-fil et de la rotation du mandrin, garantissant une meilleure répartition des forces.
- Enroulement polaire : Ce procédé est utilisé pour les pièces aux extrémités sphériques, comme les réservoirs haute pression ou les équipements spatiaux. Les fibres sont enroulées sans discontinuité grâce à des mandrins spéciaux dotés de trois degrés de liberté en rotation, permettant de suivre des géométries complexes.
Les avantages du pullwinding
Le pullwinding se distingue par sa capacité à produire des structures robustes et légères adaptées à des usagers variés, des tuyaux industriels aux réservoirs destinés à des applications exigeantes comme l'aérospatiale ou le stockage de gaz sous haute pression. En combinant différents types d'enroulements, cette technologie permet d'ajuster avec précision les propriétés mécaniques des profilés en fonction des besoins spécifiques de chaque application.
LE MOULAGE BASSE PRESSION
Le moulage basse pression est un procédé artisanal qui repose sur une chimie précise et met en valeur le savoir-faire des équipes de production. Ce processus combine simplicité d'équipement et flexibilité, en s'appuyant sur trois éléments clés : une presse à compression, un moule et un contre-moule rigide.
Les étapes du moulage basse pression
La fabrication d'une pièce commence par la préparation des moules. Ceux-ci sont recouverts d'agents de démoulage et de gelcoat, facilitant le démoulage final tout en assurant une finition de surface optimale. Ensuite, le renfort est soigneusement positionné sur le moule en fonction des propriétés mécaniques souhaitées pour la pièce. Une fois cette étape terminée, la résine est appliquée pour imprégner les renforts.
Le moule et le contre-moule sont ensuite ajustés et placés sous une presse à compression opérant avec une pression inférieure à 5 bars. Contrairement à d'autres techniques, le processus ne nécessite pas de chauffage externe, la chaleur générée naturellement par la polymérisation est suffisante pour consolider la pièce.
Une solution adaptée aux pièces complexes
Le moulage basse pression se distingue par sa capacité à produire des pièces aux géométries variées et aux dimensions sur mesure. Ce procédé permet d'obtenir des propriétés mécaniques spécifiques, adaptées aux besoins des utilisateurs. En outre, il est particulièrement économique en termes d'investissement en outillage, ce qui en fait une solution idéale pour les pièces de grandes dimensions ou aux formes complexes.
Avantages du moulage basse pression
- Flexibilité : Convient à des géométries complexes ou de grandes superficies.
- Economie : Nécessite peu d'investissement en équipement.
- Performance mécanique : Offre des propriétés sur mesure grâce à un contrôle précis du renfort et de la résine.
LE MOULAGE HAUTE PRESSION
Le moulage haute pression se distingue par sa capacité à répondre aux exigences des productions en grandes séries. Contrairement au procédé basse pression, il offre des cadences de fabrication élevées, mais implique des investissements significatifs dans des outillages spécialisés. Ce procédé repose sur l'utilisation de presses hydrauliques et de moules métalliques chauffants, assurant une efficacité et une précision accrues.
Les étapes du moulage haute pression
La préparation initiale des moules suit un processus similaire à celui du moulage basse pression. Les moules et contre-moules sont recouverts d'agents de démoulage, et les renforts sont soigneusement disposés selon les propriétés souhaitées.
La principale différence réside dans l'ajout de la résine. Dans le cas du moulage haute pression, la résine catalysée est directement versée en grande quantité sur les renforts. La répartition homogène de la résine est obtenue grâce à des cycles de descente et de pressage effectués par la presse hydraulique. Ces cycles sont ajustés en fonction de l'épaisseur des pièces et de la réactivité chimique de la résine utilisée.
Des performances adaptées aux grandes échelles
Le moulage haute pression se révèle particulièrement performant pour la fabrication de pièces en grande série nécessitant des propriétés mécaniques précises et une qualité constante. Le temps de pressage, couplé à la gestion thermique des moules métalliques chauffants, permet d'optimiser la polymérisation et d'accélérer la production sans compromettre la fiabilité des pièces.
Avantages du moulage haute pression
- Productivité élevée : Idéal pour les grandes séries.
- Précision et homogénéité : Assure une répartition uniforme de la résine et des propriétés constantes.
- Robustesse : Repose sur des presses hydrauliques et des moules chauffants pour des performances optimales.